Finishing: The Science of Ironing
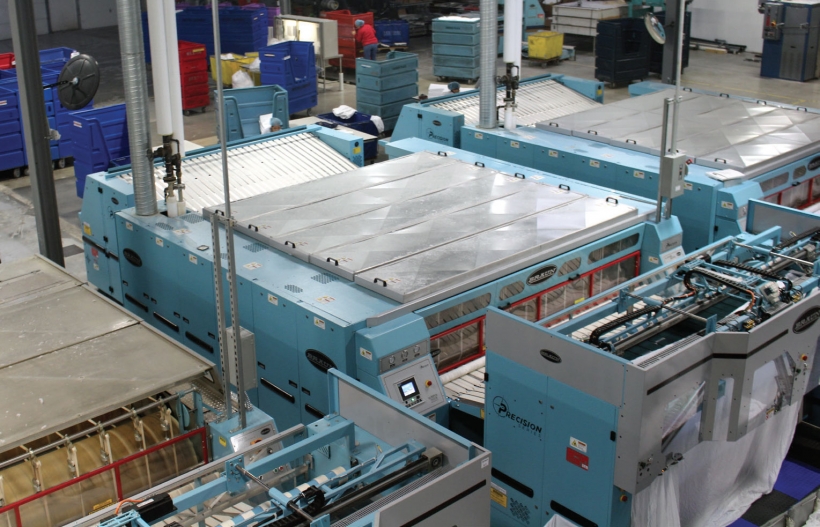
ABOVE: An overview of three ironers operating in a plant that processes primarily hospitality goods.
Keeping ironers optimized from a utilization and maintenance perspective is the best way to realize an ROI from a textile finishing line. As we review the science behind the ironing process, a simple model (Figure 1: Ironing Pie®) is used to depict the four major variables that dictate capability. This article will explain the science behind these components. Although brief, this description of the “Ironing Pie” is an important concept to understand. It is critical that laundry operators understand the relationship between each piece, so that they can properly establish formulas for processing linens in an efficient and cost-effective manner.
The four Ironing Pie components; temperature, moisture content, pressure and time are shown as equals only as a point of reference. Equal and balanced distribution of the four elements is not the case in a true ironing application.
IRONING TEMPERATURE
Heat inarguably has the single-most direct impact on an ironer’s ability to press fabric. Heat as a variable must be valued as the chest surface working temperature. The most common temperature range is from 325°–365°F ([162°–185°C] ideal operating range based on the heat source and the melt points of various blended materials). The most common form of ironer heat energy is steam, given that most laundry facilities already have boilers and the capacity to support the steam demands of the ironer (it should be noted that steam boilers run more efficiently when they have the proper load placed on them). Steam ironers tend to operate in the 325°–340°F (162-171°C) range, while thermal fluid heated units can operate at higher temperatures. Variations in chest temperatures during production can result in poor ironed quality with damp/wet items exiting the ironer, while prolonged exposure to extreme high temperatures can damage items.
This magnifies the importance of having a consistent moisture content in the linens as they are presented to the finishing lines. By doing so, established formulas will provide consistent quality and production output.
When establishing formula operating temperatures, it’s recommended to consult your linen provider for guidance on how to properly care for your items. Knowing the items’ maximum recommended exposure for temperature is always an important point to consider. The most common configuration is to operate the ironer as hot as possible and adjust line speed to control an item’s exposure to heat.
Once an ironer’s maximum operating temperature is established, any reduction in chest-surface temperatures will increase the time required for the items to be under pressure, resulting in slower line speeds. To offset operating at a slower line speed, other pieces of the Ironing Pie must be addressed. You can reduce the items’ moisture content by increasing your extraction times, or extraction time under pressure (depending on how the linens are washed in conventional washer/ extractors, or if they are processed in batch tunnels). Additionally, you can positively influence line speeds to address higher moisture content by adding additional rolls/surface area to your ironer.
MATERIALS MOISTURE CONTENT
Moisture Content is a key component in the Ironing Pie. It starts as a weighted comparison of a linen’s ability to retain moisture after undergoing processing through a press or washer/extractor cycle. This is achieved by weighing dry linens before being washed and again after the linens have been processed as delivered to the finishing line ready for ironing. Moisture content can then be calculated by following the formula below:
It’s recommended that items contain 30%-40% moisture content before ironing. Adhering to this guideline will help ensure a quality ironed finish, while minimizing linen damage. It’s true that a reduction in an item’s moisture content is directly related to increased processing line speed under temperature as noted above. But fully dried items should not be processed through an ironer. Attempting to achieve lower extraction percentages might not be practical as a scale of diminishing returns will occur with no value added. Every site is different and each needs to qualify its own capabilities for this measure. When a site is having issues controlling moisture content, pre-conditioning loads in a dryer is another process that operators can consider. What’s important is to develop a process of producing repeatable moisture content for items processed on the front end of the finishing line. Items exiting the ironer should maintain 2-3% moisture content, as this will allow smooth folds and preserve the life of the fibers, while reducing the creation of lint and static electricity. Items ironed fully dry without moisture retention present are prone to fiber damage, excessive accumulation of lint and the creation of high levels of static electricity. Increased front-end item moisture content will increase the amount of time required for an item to be under pressure, resulting in slower line speeds, which decreases throughput. To offset the impact of slower line speeds, increasing chest temperature and the contact area under pressure will help restore line speed. When chest temperature is operating at the highest potential for output, preconditioning select items has the potential to reduce moisture content, inversely restoring an ironing line’s capability for throughput. It should be noted that discharging items with elevated moisture content will typically result in poor fold quality, folding equipment jams and unplanned operational downtime. Also, it can present a hygienic liability as mold can grow on damp linens that are stored or packaged for shipment to the end user.
IRONING CONTACT PRESSURE
The Ironing Pie defines pressure as the location where the padded roll applies pressure onto a sheet against a deep chest simultaneously. There are two components to pressure: The first is the surface area under pressure, which is dictated by the size of the roll utilized and the number or rolls with which the ironer is configured. The other pressure variable is the applied surface physical force between an ironer roll and its respective chest surface. The first pressure variable is established at the time of equipment purchase, often within the customer bid specification, which defines specific site-configuration factors and performance throughput. Ironer OEMs are best suited to provide guidance in sizing an ironer, since each manufacturer will understand the impact and limitation regarding the contact area under pressure and how their ironer will perform. It’s debatable whether the use of this term might have been over-marketed. Simply put, an operator should look at the size of the ironing surface as a linear value and not the accumulative total area of square inches/centimeters. It’s necessary to understand that the impact of the contact area under pressure is fixed to the number and size of rolls utilized. It is not recommended to leverage this value as the single qualifier for ironer performance, or to justify the purchase of similar-sized two- or three-roll ironers. Many additional factors require consideration (e.g., chest type, construction, design, number of rolls and size of rolls all need to be part of the selection process). Make sure to use all factored inputs to correctly define ironing needs. A good up-front purchasing decision establishes a flatwork line return on investment for years to come.
IRONING DURATION OF TIME
The Ironing Pie defines time as three different variables. The duration of time for each variable is site-specific and all are impacted by the factors identified in the Ironing Pie. They include:
- Start Up Time
- Production Time Under Pressure
- Cool Down Time
Key input factors specific to ironer time are desired operating temperature, items processed, moisture content and contact pressures.
START UP TIME is the duration of time required to raise the temperature of the ironer from its current static or ambient temperature up to “hot” wax-ready operating temperature. This segment of time is directly dependent on the type of ironer, specifically its heat source with respect to starting chest temperatures. During this time most laundries will execute a wax procedure and will replace any missing guide ribbons so that when complete, the ironer is production ready.
PRODUCTION TIME UNDER PRESSURE is the segment of time when the ironer is hot at operational temperature and available to run flatwork production. This is when equipment utilization becomes a measurable, and where an ROI can be verified while looking for opportunities for improvement. A good approach is to tune the ironer line speed for sustainable site operations that is item-specific for predictable, repeatable results. During the utilization review, note all identified shortcomings. Some can be resolved as tuning opportunities, while others may be fixed constraints requiring a more complex series of solutions. A good objective should be to keep the ironer chest covered with items and processing with minimal gaps. Items should exit the ironer with 2%-3% moisture retention to prevent static electricity, producing a quality ironed, wrinkle-free appearance. Avoid attempting to configure line speeds to operate beyond the slowest piece of equipment or at full boiler capacity. Some cushion is required to absorb momentary changes in the plant- operating environment. Time under pressure is the amount of time that the ironer roll is pressing items into a hot chest. This value has a direct relationship to the amount of fixed contact area under pressure. The longer this linear contact pressure distance is, the less time under pressure is required to iron. Other factors that can impact time under pressure are fabrics. For example, 100% cotton will require more time under pressure than a cotton/poly blend or microfiber.
COOL DOWN TIME is the time period to lower the temperature of the ironer from operating speeds down to cooler “touch- safe” temperatures. It’s obvious that cool down times will be affected by operating temperature and the type of medium used to heat the ironer, as well as the size of the ironer itself. Even if your daily operations never fully shut down laundry boilers, it’s important to qualify the time required to cool the system for servicing the unit and restarting. Certain preventive maintenance (PM) and servicing activities should not be attempted on a hot ironer (e.g., replacing spring press, padding rolls, servicing traps/gaskets/ flanges).
The science of ironing has changed very little over the years. Rather, it is the application of technology, equipment de- signs, the heat sources used and configurations of deep chest ironers that have evolved to support the demands of the market/industry. In today’s modern laundries, the capability of the ironer is typically what dictates the production capacity of the processing line.
AUTHOR’S NOTE: “Ironing Pie®” is a registered trademark of G.A. Braun Inc
BRYAN KNAPICK is a finishing equipment engineer for ironing technology at G.A. Braun, Inc., Syracuse, NY.
Contact him at bknapick@gabraun.com.