Safety is integrated into every aspect of a Braun project. It is a consideration at every stage of project development and execution. Braun is committed to ensuring that all personnel remain safe during all project phases in laundry operations.
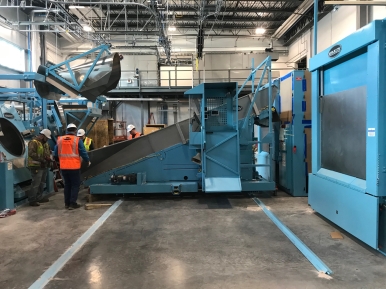
The process starts with the initial review of the specific laundry operation during the promotion of a Braun equipment solution. Site assessment includes reviewing unusual hazards or areas of special consideration from a constructibility and risk potential perspective. Risks and hazards identified are researched for alternatives to mitigate exposure. When estimating resources, safety concerns are included. Work plans are reviewed by senior management, including safety personnel, with a goal of reducing employee exposure to hazards.
Project preplanning begins once a specific opportunity is committed to Braun, and resources are matched to project needs. Project Management personnel are selected who have experience and can lead in the field. Equipment is secured that fits best practice for site conditions. Subcontractors are selected who can implement a safe and compliant work plan.
A site-specific safety plan is then developed to match the project. Onsite Project Managers and Project Field Supervisors assume the role of onsite safety management and tailor the plan. Safety rules and regulations are included for anticipated activities. Specifics for personnel, contacts, and local emergency response are inserted.
Project Managers meet with Braun Field Service Technicians and selected subcontractors to discuss project needs. Training requirements are matched to the skill set required for a safe and productive project.
Employees onsite for the first time receive orientation and project-specific training before starting work on the project. Project Managers and Project Field Supervisors manage daily activities and ensure that subcontractors and Braun Field Service Technicians are adhering to the proper safety guidelines. On-site training and mentoring are provided as needed.
Personal protective equipment (PPE) is issued to all employees and subcontractors and is required to be worn by personnel while onsite.Field Service Technicians and Subcontractors meet daily with Project Management, before the workday begins, to review upcoming activities and safety concerns. Jobsite conditions and hazards previously identified are shared by crews working in an area previously.
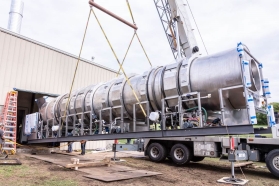
Subcontractors gather each day to complete a Job Safety Analysis and toolbox talk. Conditions and hazards associated with the planned activities are discussed along with the necessary mitigation. A database of activities, hazards, and abatement techniques has been developed by Project Field Supervisors, Project Managers, and safety professionals. Additions are made to the supplied checklist as needed, and onsite personnel sign in to document attendance.
Equipment is inspected each day before use. Fueling and maintenance are performed with proper protective measures.
Daily and weekly project updates are communicated to the Director, Inside Sales & Project Management, as well as the Safety & Environmental Risk Manager. Project status and planned activities are reviewed. Incidents from the previous week are discussed, along with lessons learned, to avoid repeating incidents. The Site-Specific Safety Plan is updated with any changes in site conditions and tasks.
This is an example of a job safety analysis plan from Braun for a recent on-premise laundry project in the healthcare industry:
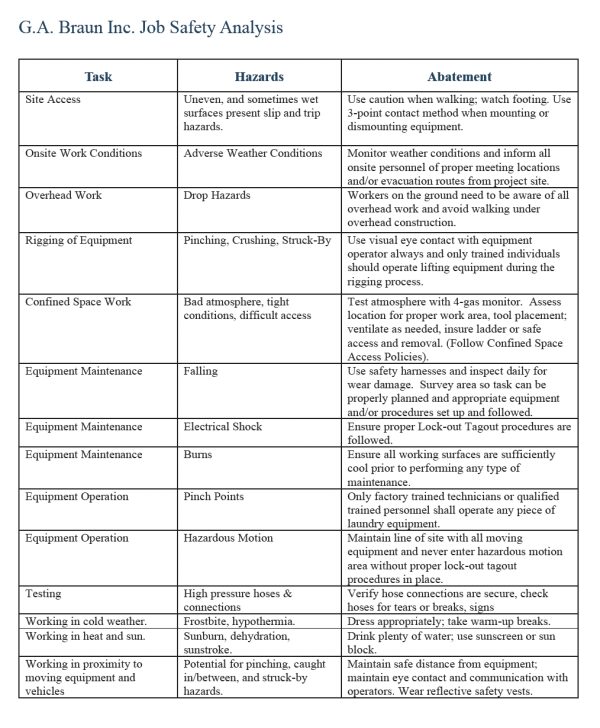
By Cliff Quick, Director of Inside Sales and Project Management at G.A. Braun Inc.
Learn more in our Project Management Guide: Click Here